Episodes
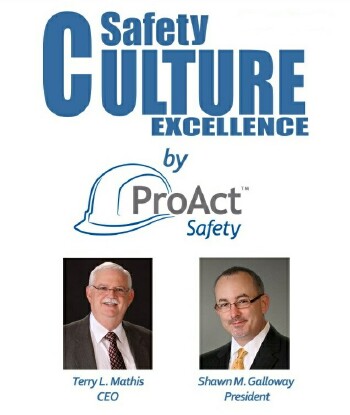
Monday May 16, 2016
440: Five Reasons You Have Undesired Performance
Monday May 16, 2016
Monday May 16, 2016

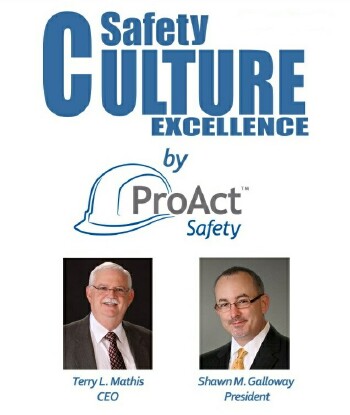
Monday May 02, 2016
438: The True Goal of an Effective Safety Program
Monday May 02, 2016
Monday May 02, 2016

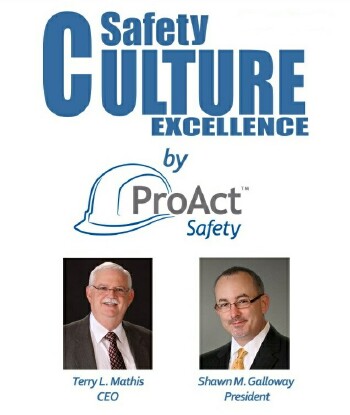
Monday Jan 04, 2016
Monday Jan 04, 2016

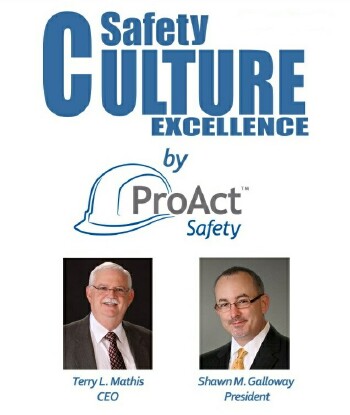
Monday Dec 07, 2015
417: 4 Types of Safety Behaviours (Culture Shock Video)
Monday Dec 07, 2015
Monday Dec 07, 2015

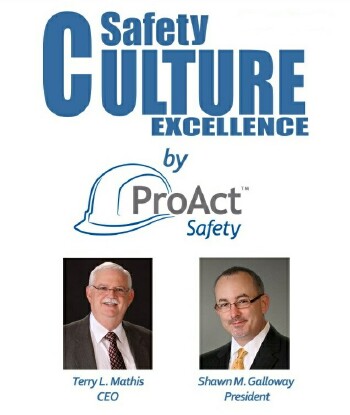
Monday Nov 30, 2015
416: How Portable Are Your Safety Efforts?
Monday Nov 30, 2015
Monday Nov 30, 2015

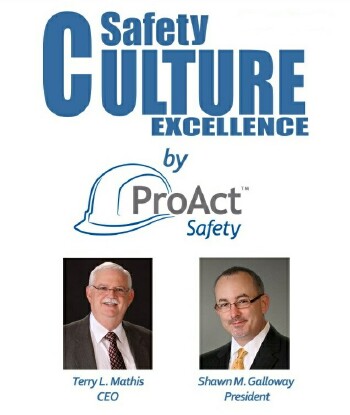
Monday May 18, 2015
388 - The Only Way Safety Will Continuously Improve
Monday May 18, 2015
Monday May 18, 2015
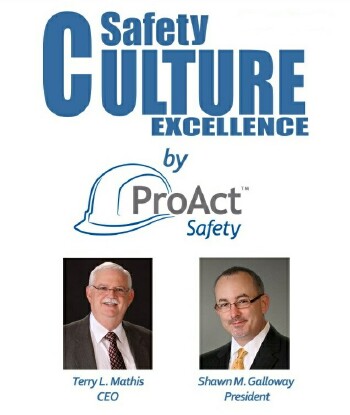
Wednesday Apr 29, 2015
Peeling the Onion: Solving Safety Problems One Layer at a Time
Wednesday Apr 29, 2015
Wednesday Apr 29, 2015
During a safety observation, workers were observed using the wrong tool for a job, which created a risk. When a safety committee saw the report, they petitioned management to buy the proper tool for the work station. The committee member who received the tool took it to the work station and presented it to the worker on shift with an explanation of what had happened and the action taken. The worker admitted that he really had not been taught what the proper tool was for the job and had used the home-made tool since he began his job.
The next month’s observations reported that workers were still using the wrong tool for the job. Follow-up revealed that workers on the other shifts had not received the communication and were not aware of the new tool. The safety committee made sure that every worker was made aware of the proper tool in safety and tool box meetings and felt sure the next month’s data would show the problem solved.
The next month, the observations showed the workers were STILL not using the right tool. Follow-up revealed that workers had formed the habit of using the wrong tool and that the habit was not changed. The safety committee developed a plan to remind workers and, within the next few months, the problem was truly solved.
Lessons learned:
• Safety problems can be multi-layered and require multiple fixes.
• Solving problems requires follow-up.
• Influences need to be addressed in order to change the behavior.
-Terry L. Mathis
For more insights, visit
www.ProActSafety.com
Terry L. Mathis is the founder and CEO of ProAct Safety, an international safety and performance excellence firm. He is known for his dynamic presentations in the fields of behavioral and cultural safety, leadership, and operational performance, and is a regular speaker at ASSE, NSC, and numerous company and industry conferences. EHS Today listed Terry as a Safety Guru in ‘The 50 People Who Most Influenced EHS three consecutive times. He has been a frequent contributor to industry magazines for over 15 years and is the coauthor of STEPS to Safety Culture Excellence (2013, WILEY).
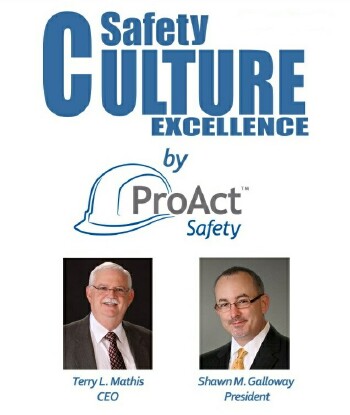
Wednesday Apr 08, 2015
Training vs. Education
Wednesday Apr 08, 2015
Wednesday Apr 08, 2015
More and more organizations are using computer-based training (CBT) modules. Most started using them for OSHA-required yearly refresher training. The CBT approach had some advantages: workers could attend individually rather than in a classroom with multiple students and an instructor; the individual training approach caused less disruption of business activities than a classroom approach; the training was self-paced so everyone could move through the materials at their own pace; the modules could include testing for knowledge levels; and the CBT could keep current rosters of who had completed the various modules.
Then organizations expanded the use of CBT into more questionable areas. Along this path, someone forgot that CBT is education; not training. You can impart information via computer but you cannot build manual skills. Relying on CBT to teach manual job skills or even basics such as fire-extinguisher use is only a partial approach. Students end up having knowledge without skills. If the CBTs are followed up with on-the-job training or classroom simulations, the knowledge can begin to be translated into skills. Without such follow-up, CBTs can simply create a false sense of competence that can, and has, resulted in serious safety incidents.
-Terry L. Mathis
For more insights, visit
www.ProActSafety.com
Terry L. Mathis is the founder and CEO of ProAct Safety, an international safety and performance excellence firm. He is known for his dynamic presentations in the fields of behavioral and cultural safety, leadership, and operational performance, and is a regular speaker at ASSE, NSC, and numerous company and industry conferences. EHS Today listed Terry as a Safety Guru in ‘The 50 People Who Most Influenced EHS three consecutive times. He has been a frequent contributor to industry magazines for over 15 years and is the coauthor of STEPS to Safety Culture Excellence (2013, WILEY).
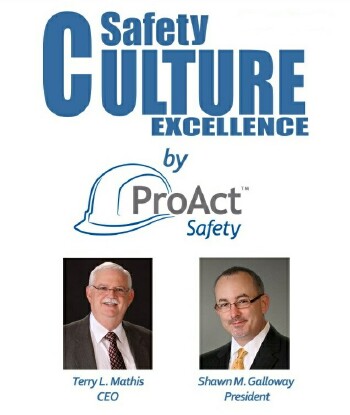
Wednesday Apr 01, 2015
Probability: Group Experience
Wednesday Apr 01, 2015
Wednesday Apr 01, 2015
A worker using the wrong tool for a job injures his hand. Another worker has used the same wrong tool numerous times with no injury. One worker retires having used this tool his whole career with no injury and another retiree has had three injuries related to using that tool. Each experience is different, and thus, each perception of the risk is different. Some think the practice is dangerous and some think it is not. Who is right and who is wrong?
We express a range of experience mathematically by calculating probability. With enough data points we can establish a pattern to this risk that may not be obvious to anyone who is a data point, but is accurately describing the experience of the large group. Sharing the findings of a probability study can actually change and norm the perceptions formed by differing experiences within the group. This new perception can more accurately describe the risk and encourage taking precautions against the risk even among those whose experience hasn’t detected the possibility of accidental injury. Perceptions, if not thus managed, will vary by experience. Managing the accuracy of perceptions is a powerful tool for improving safety performance that many organizations have not utilized.
-Terry L. Mathis
For more insights, visit
www.ProActSafety.com
Terry L. Mathis is the founder and CEO of ProAct Safety, an international safety and performance excellence firm. He is known for his dynamic presentations in the fields of behavioral and cultural safety, leadership, and operational performance, and is a regular speaker at ASSE, NSC, and numerous company and industry conferences. EHS Today listed Terry as a Safety Guru in ‘The 50 People Who Most Influenced EHS three consecutive times. He has been a frequent contributor to industry magazines for over 15 years and is the coauthor of STEPS to Safety Culture Excellence (2013, WILEY).
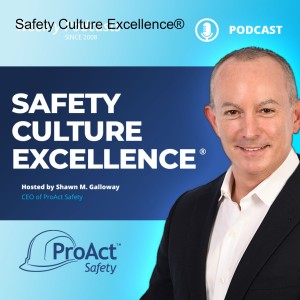
Monday Mar 02, 2015
377 - The Reality of Positive Reinforcement
Monday Mar 02, 2015
Monday Mar 02, 2015
