Episodes
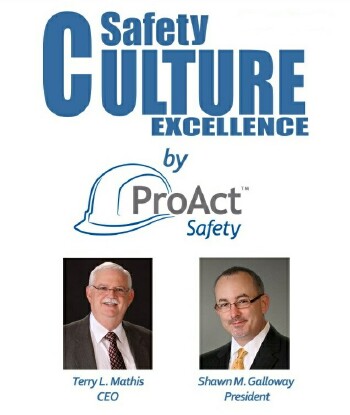
Monday Jan 04, 2016
Monday Jan 04, 2016

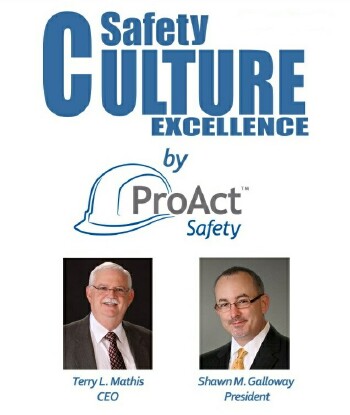
Monday Dec 28, 2015
420: It's No Surprise We Fail Our Supervisors
Monday Dec 28, 2015
Monday Dec 28, 2015

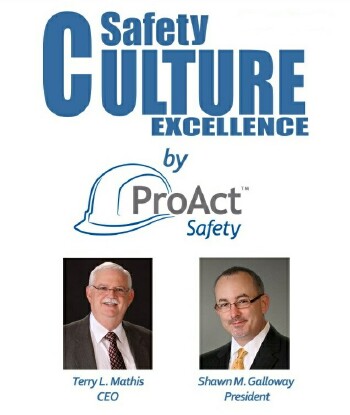
Monday Nov 02, 2015
412 - Fear: The Enemy of Safety Excellence
Monday Nov 02, 2015
Monday Nov 02, 2015

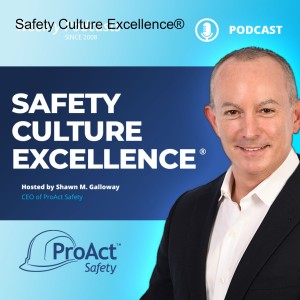
Wednesday Jun 10, 2015
How Effective Is Your Management of Change System?
Wednesday Jun 10, 2015
Wednesday Jun 10, 2015
The Center for Chemical Process Safety (CCPS) defines Management of Change (MOC) as:
“A temporary or permanent substitution, alteration, replacement (not in kind), modification by addition or deletion of critical process equipment, applicable codes, process controls, catalysts or chemicals, feed stocks, mechanical procedures, electrical procedures, safety procedures, emergency response equipment from the present configuration of the critical process equipment, procedures, or operating limits.”
Or as stated by the U.S. Chemical Safety and Hazard Investigation Board (CSB):
“In industry, as elsewhere, change often brings progress. But it can also increase risks that, if not properly managed, create conditions that may lead to injuries, property damage or even death.”
On June 1, 1974, the Nypro cyclohexane oxidation plant in Flixborough, England was destroyed by an explosion. There was a release of 30 tons of cyclohexane to the atmosphere that formed a vapor cloud ignited by an unknown source about 45 seconds after the release. The resulting explosion destroyed the entire plant, resulting in the death of 28 people and 89 other serious injuries. The number of fatalities would have been much greater had the accident occurred on a weekday when the administrative offices would have been filled with employees. The damage extended beyond the plant to 1,821 nearby houses and 167 shops and factories; total property damage reached $63 million.
The Flixborough explosion was the result of an unwise plant maintenance modification. In short, there was no MOC process in place, and it was as a result of this incident that the regulators such as HSE introduced MOC as part of Plant Safety regulations (i.e. COMAH in the UK). If an MOC system has been in effect at the plant, the explosion might have been prevented. The MOC system would have called for a proper safety review, adequate approval at all stages of the change process, and a design created by trained professionals.
One of the main recommendations of the Flixborough inquiry was:
“Any modification should be designed, constructed, tested, and maintained to the same standards as the original plant.”
Many of our safety regulations, analysis methodologies, and technologies that we use today have evolved as a result of incidents such as Flixborough, Piper Alpha, Bhopal, and many more.
Thankfully, not all MOC related incidents are as severe as Flixborough, but these minor day-to-day infractions should be a big red flag, as they nevertheless have an impact on an organization. If not resolved, they are likely to result in far more severe consequences.
MOC and related permit to work activities can be viewed as a burden on Operations and Maintenance personnel who are already working overtime on managing their daily activities of running the facility efficiently. However, MOCs must be implemented in a robust fashion and appropriate resources must be allocated.
The number of MOC a typical plant processes can be summarized in the following statements by Ian Sutton Ref (Process Risk and Reliability Management June 2009 http://www.stb07.com/):
- 250 MOCs per year for a medium-sized site of say 140 employees
- 1,000 MOCs per year for a large site of say 2000 employees
- 1,400 MOCs for a world scale Refinery
How good is your MOC system, and can you safely and efficiently handle the MOCs in your facilities? Take into consideration the following questions:
- Can your MOC system provide the following Key Performance Indicators (KPIs)?
- Percentage of MOCs past due date
- Percentage of MOCs properly executed
- Percentage of audited changes that used MOC prior to making the change
- Number Temporary changes still to be MOC-ed
- Number MOC performed per month, and monthly average
- Percentage of work requests classified as a change
- Percentage or variation in the number of changes processed on an emergency basis
- Average backlog of MOCs/active MOCs
- Average time taken between MOC origination & authorization
- Percentage of work orders/requests that were misclassified as replacement-in-kind (RIK) but should have been MOCs
- Ratio of identified undocumented changes to number of changes processes by MOC
- Percentage of changes that were MOC-ed but reviewed incorrectly
- Percentage of MOCs that were not documented properly
- Percentage of MOCs for which drawings and procedures were not updated
- Percentage of temporary MOCs where the temporary conditions were not corrected/restored to original state by the deadline
- (#MOCs/#MOCs+#changes that by-passed MOC) *100%
- Can you conduct a complete and thorough impact assessment to show all related data and information that needs to be reviewed and re-validated as a result of the proposed MOC (e.g. trip and alarm setting, procedures, LOTO, cause and effect diagrams, etc.)?
If you can confidently answer yes to these questions, you have a robust system in place and are in control. If not, we recommend reevaluating your MOC processes to help ensure your MOC system can effectively and safely process the large volume of MOCs that may flow through your facilities.
This has been a guest contribution by Clive Wilby.
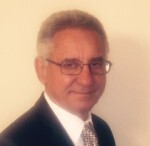
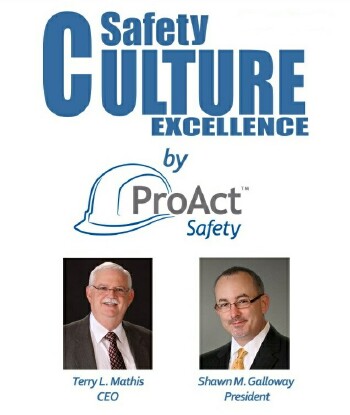
Monday May 18, 2015
388 - The Only Way Safety Will Continuously Improve
Monday May 18, 2015
Monday May 18, 2015
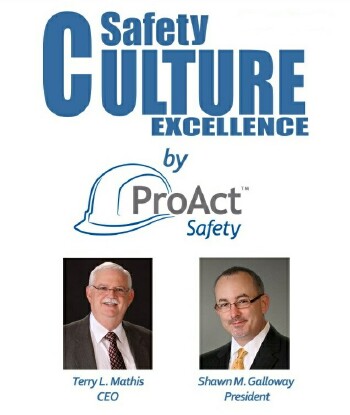
Wednesday May 13, 2015
Self-Awareness: The Short-Cut to Greatness
Wednesday May 13, 2015
Wednesday May 13, 2015
Since the beginning of time, successful people around the world have shared similar personality characteristics.
Martin Luther King inspired a movement with his ability to instill emotion in his fellow people. Winston Churchill made a war-torn nation stand up with confidence and fight a seemingly unstoppable enemy. Mahatma Ghandi used civil disobedience to change the world for Indians, at home and in South Africa. Steve Jobs inspired a technological revolution with creativity and an uncanny knack for capturing an audience.
Behavioral science will tell you that these great people had specific personality characteristics that led them to behave in the way they did. Research into psychology and personality will provide evidence that they were great because they were born great.
But what about the rest of us?
Chances are, you may consider yourself a bit more “ordinary” than the leaders of history. However, you have the potential to achieve your own personal greatness.
Through self-awareness, we can learn how to interrupt our natural default behaviors that keep us from behaving in a way that is productive, efficient, and safe. By taking control of our own self-awareness and truly understanding who we are underneath it all, we can achieve our own greatness in our own lives. The only thing holding us back is ourselves.
Take one of my friends for instance. He was not a social person by birth; he has consciously developed the skills of communication and education to a point that those who meet him would describe him as a talkative and very pleasant person. Little do they know that he exerts a significant amount of energy in social situations - far less than people like him who naturally derives great pleasure from social interaction.
How did he do it? Through a heightened sense of self-awareness.
If my friend recognized that he was uncomfortable in a situation, he would remind himself of why it’s important that he develops these skills. In times of stress or confusion, when his natural default personality was at its strongest, he learned to be in control, behave in the way he wanted to, and ignore his sometimes risky gut reactions.
You too can rise to new heights by first learning why you act the way you do. Through this self-reflection you can leverage your innate strengths to improve your decision making and behavior both at work and at home.
This has been a guest contribution by Greg Ford.
Greg is the co-founder and CEO
of TalentClick Workforce Solutions
and an adjunct professor at Simon Fraser University in Vancouver, Canada. Greg
holds a degree in Psychology and a Master’s degree in Workplace Learning. He is
the co-author of the safety book “Before It Happens” and has spoken at conferences
across North America.
You can discover the power of Safety Self-Awareness with a free 30 day unlimited subscription of TalentClick’s full suite of safety solutions, including self-study, online training, and personalized coaching by going to http://www.talentclick.com/gb-trial/.
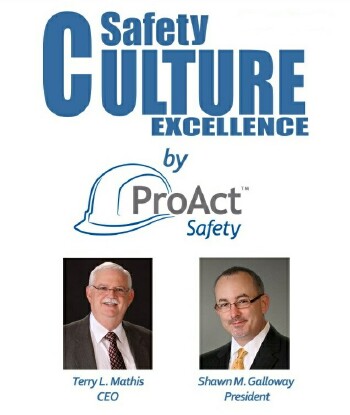
Wednesday Apr 29, 2015
Peeling the Onion: Solving Safety Problems One Layer at a Time
Wednesday Apr 29, 2015
Wednesday Apr 29, 2015
During a safety observation, workers were observed using the wrong tool for a job, which created a risk. When a safety committee saw the report, they petitioned management to buy the proper tool for the work station. The committee member who received the tool took it to the work station and presented it to the worker on shift with an explanation of what had happened and the action taken. The worker admitted that he really had not been taught what the proper tool was for the job and had used the home-made tool since he began his job.
The next month’s observations reported that workers were still using the wrong tool for the job. Follow-up revealed that workers on the other shifts had not received the communication and were not aware of the new tool. The safety committee made sure that every worker was made aware of the proper tool in safety and tool box meetings and felt sure the next month’s data would show the problem solved.
The next month, the observations showed the workers were STILL not using the right tool. Follow-up revealed that workers had formed the habit of using the wrong tool and that the habit was not changed. The safety committee developed a plan to remind workers and, within the next few months, the problem was truly solved.
Lessons learned:
• Safety problems can be multi-layered and require multiple fixes.
• Solving problems requires follow-up.
• Influences need to be addressed in order to change the behavior.
-Terry L. Mathis
For more insights, visit
www.ProActSafety.com
Terry L. Mathis is the founder and CEO of ProAct Safety, an international safety and performance excellence firm. He is known for his dynamic presentations in the fields of behavioral and cultural safety, leadership, and operational performance, and is a regular speaker at ASSE, NSC, and numerous company and industry conferences. EHS Today listed Terry as a Safety Guru in ‘The 50 People Who Most Influenced EHS three consecutive times. He has been a frequent contributor to industry magazines for over 15 years and is the coauthor of STEPS to Safety Culture Excellence (2013, WILEY).
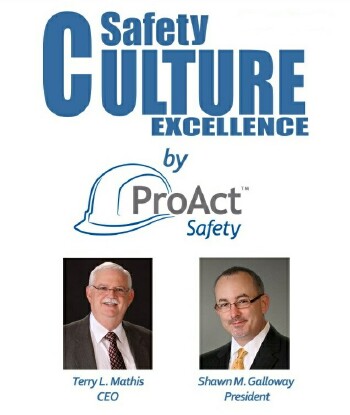
Wednesday Apr 22, 2015
Factor-Finding Failures
Wednesday Apr 22, 2015
Wednesday Apr 22, 2015
When new safety programs or processes are rolled out unsuccessfully, there has almost always been a failure to determine either the factors necessary for success, the factors that can contribute to failure, or some combination of both. Without a list of the key factors of success and failure, a project launch is a blind affair. This blindness seems more logical if the project appears to be well constructed and has been successful at other organizations or sites in the same organization. Sadly, imitation of success is no guarantee of success.
The reasons for the imitation failing are basically the differences in sites and cultures. A good fit for one site might be a recipe for disaster at another. That is why an analysis of success and failure factors is so necessary. Such an analysis is unique to each culture. It should include a review of past successes and/or failures and the factors that contributed to those; but it should also include simply asking a representative cross-sample of people what they think of the project and what it would take to make it work. Good implementers and change agents have usually learned a lot about such analysis, but can almost always be more thorough if they simply list critical factors to success and failure, and address them in their implementations.
-Terry L. Mathis
For more insights, visit www.ProActSafety.com
Terry L. Mathis is the founder and CEO of ProAct Safety, an international safety and performance excellence firm. He is known for his dynamic presentations in the fields of behavioral and cultural safety, leadership, and operational performance, and is a regular speaker at ASSE, NSC, and numerous company and industry conferences. EHS Today listed Terry as a Safety Guru in ‘The 50 People Who Most Influenced EHS three consecutive times. He has been a frequent contributor to industry magazines for over 15 years and is the coauthor of STEPS to Safety Culture Excellence (2013, WILEY).
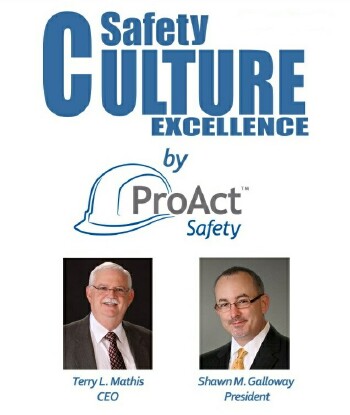
Wednesday Apr 08, 2015
Training vs. Education
Wednesday Apr 08, 2015
Wednesday Apr 08, 2015
More and more organizations are using computer-based training (CBT) modules. Most started using them for OSHA-required yearly refresher training. The CBT approach had some advantages: workers could attend individually rather than in a classroom with multiple students and an instructor; the individual training approach caused less disruption of business activities than a classroom approach; the training was self-paced so everyone could move through the materials at their own pace; the modules could include testing for knowledge levels; and the CBT could keep current rosters of who had completed the various modules.
Then organizations expanded the use of CBT into more questionable areas. Along this path, someone forgot that CBT is education; not training. You can impart information via computer but you cannot build manual skills. Relying on CBT to teach manual job skills or even basics such as fire-extinguisher use is only a partial approach. Students end up having knowledge without skills. If the CBTs are followed up with on-the-job training or classroom simulations, the knowledge can begin to be translated into skills. Without such follow-up, CBTs can simply create a false sense of competence that can, and has, resulted in serious safety incidents.
-Terry L. Mathis
For more insights, visit
www.ProActSafety.com
Terry L. Mathis is the founder and CEO of ProAct Safety, an international safety and performance excellence firm. He is known for his dynamic presentations in the fields of behavioral and cultural safety, leadership, and operational performance, and is a regular speaker at ASSE, NSC, and numerous company and industry conferences. EHS Today listed Terry as a Safety Guru in ‘The 50 People Who Most Influenced EHS three consecutive times. He has been a frequent contributor to industry magazines for over 15 years and is the coauthor of STEPS to Safety Culture Excellence (2013, WILEY).
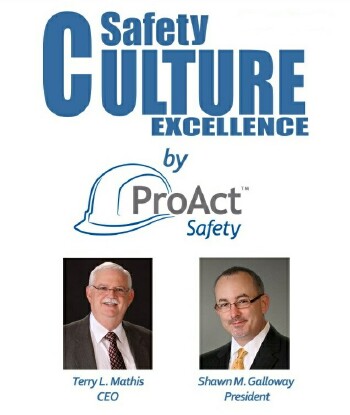
Wednesday Apr 01, 2015
Probability: Group Experience
Wednesday Apr 01, 2015
Wednesday Apr 01, 2015
A worker using the wrong tool for a job injures his hand. Another worker has used the same wrong tool numerous times with no injury. One worker retires having used this tool his whole career with no injury and another retiree has had three injuries related to using that tool. Each experience is different, and thus, each perception of the risk is different. Some think the practice is dangerous and some think it is not. Who is right and who is wrong?
We express a range of experience mathematically by calculating probability. With enough data points we can establish a pattern to this risk that may not be obvious to anyone who is a data point, but is accurately describing the experience of the large group. Sharing the findings of a probability study can actually change and norm the perceptions formed by differing experiences within the group. This new perception can more accurately describe the risk and encourage taking precautions against the risk even among those whose experience hasn’t detected the possibility of accidental injury. Perceptions, if not thus managed, will vary by experience. Managing the accuracy of perceptions is a powerful tool for improving safety performance that many organizations have not utilized.
-Terry L. Mathis
For more insights, visit
www.ProActSafety.com
Terry L. Mathis is the founder and CEO of ProAct Safety, an international safety and performance excellence firm. He is known for his dynamic presentations in the fields of behavioral and cultural safety, leadership, and operational performance, and is a regular speaker at ASSE, NSC, and numerous company and industry conferences. EHS Today listed Terry as a Safety Guru in ‘The 50 People Who Most Influenced EHS three consecutive times. He has been a frequent contributor to industry magazines for over 15 years and is the coauthor of STEPS to Safety Culture Excellence (2013, WILEY).