Episodes
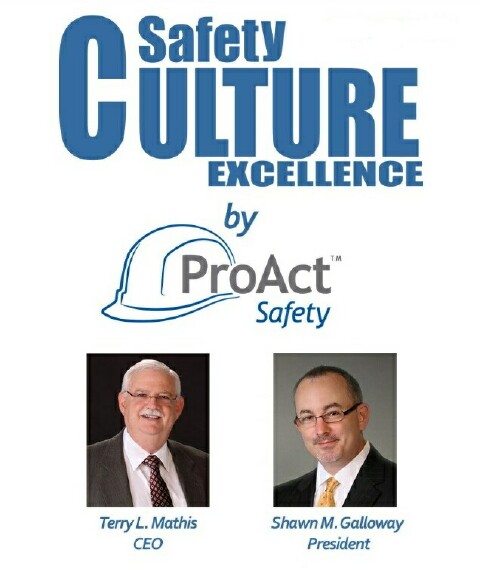
Monday Aug 18, 2014
350 - Evolving Your Safety Culture Elements That Matter Most
Monday Aug 18, 2014
Monday Aug 18, 2014
Greetings everyone, this podcast recorded while in Eunice, LA. I’d like to share an article I wrote that was published in the July 2014 edition of OH&S Magazine. The published article can either be found on the magazine’s website or under Insights at www.ProActSafety.com.
I hope you enjoy the podcast this week. If you would like to download or play on demand our other podcasts, please visit the ProAct Safety’s podcast website at: http://www.safetycultureexcellence.com. If you would like access to archived podcasts (older than 90 days – dating back to January 2008) please visit www.ProActSafety.com/Store. For more detailed strategies to achieve and sustain excellence in performance and culture, pick up a copy of our book, STEPS to Safety Culture Excellence - http://proactsafety.com/insights/steps-to-safety-culture-excellence
Have a great week!
Shawn M. Galloway
ProAct Safety
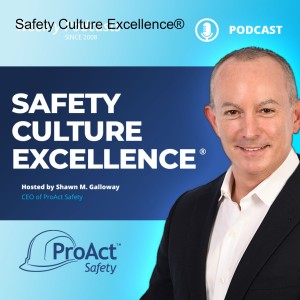
Tuesday Aug 12, 2014
STEPS to Safety Culture Excellence Workshop - October 2014
Tuesday Aug 12, 2014
Tuesday Aug 12, 2014

Based on the book, STEPS to Safety Culture Excellence, the authors will lead this workshop and provide a detailed roadmap on how to develop a three to five year safety excellence business plan. This two-day workshop is limited to ten participants. It would be helpful if each attendee read the book prior to the event to escalate the discovery process.

ProAct Safety® recently compiled data on over 1,100 sites that requested our help in improving safety. The commonalities of these sites' issues has led to a new approach to solving safety problems and permanently implementing continuous improvement. The approach includes organizational structure, problem identification, issue prioritization, action plan development, improvement metrics, and a motivational and marketing strategy to ensure sustainability. The process is called STEPS (Strategic Targets for Excellent Performance in SafetySM).
Objectives:
- Develop a solid understanding of a safety excellence strategy
- Learn the leading causes of safety program ineffectiveness and failure
- Examine a standard methodology used by excellent safety organizations to identify virtually any type of safety issue or problem
- Learn to use statistical tools to prioritize issues by their potential impact
- Learn to develop action plans to solve safety problems
- Explore innovative ways to measure success and progress
- Discover how one process can replace multiple programs and allow for seamless transition of focus without causing a flavor-of-the-month culture
Workshop Takeaways - Attendees will be provided with:
- Electronic Materials (Templates) to return to their organization and facilitate discussions for the creation of their unique safety excellence strategy.
- A 60-Minute Recorded High-Level Webinar outlining the key STEPS to Safety Culture Excellence methodologies. This will help convey the messages and build support and understanding for the necessary path forward. Moreover, this can also help during on-boarding of future leaders to provide an understanding of why the strategy was created, furthering the future support necessary as the organization continuously improves safety performance and culture and acquires or promotes new leadership talent.
- Access to Shawn M. Galloway or Terry L. Mathis from 8 am to 5 pm CT during the week by email and phone for one month following the workshop, to help support efforts by coaching and advising through the initial creation of the strategy. If not immediately available, calls and emails will be returned within 24 hours.
- A personalized autographed copy of the book, STEPS to Safety Culture Excellence.
For more information, visit this link.
See you there!
Shawn M. Galloway
ProAct Safety, Inc.
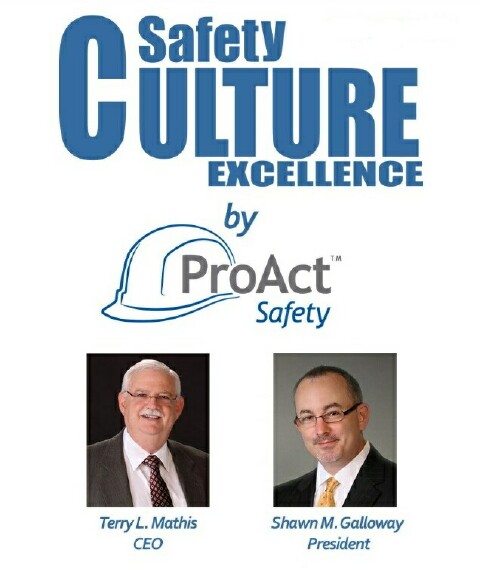
Monday Aug 11, 2014
349 - Safety Drivers The First Level of Leading Indicators
Monday Aug 11, 2014
Monday Aug 11, 2014
Greetings everyone, this podcast recorded while in Port Arthur, TX. I’d like to share an article Terry Mathis wrote that was published in the July 2014 edition of EHS Today Magazine. The published article can either be found on the magazine’s website or under Insights at www.ProActSafety.com.
I hope you enjoy the podcast this week. If you would like to download or play on demand our other podcasts, please visit the ProAct Safety’s podcast website at: http://www.safetycultureexcellence.com. If you would like access to archived podcasts (older than 90 days – dating back to January 2008) please visit www.ProActSafety.com/Store. For more detailed strategies to achieve and sustain excellence in performance and culture, pick up a copy of our book, STEPS to Safety Culture Excellence - http://proactsafety.com/insights/steps-to-safety-culture-excellence
Have a great week!
Shawn M. Galloway
ProAct Safety
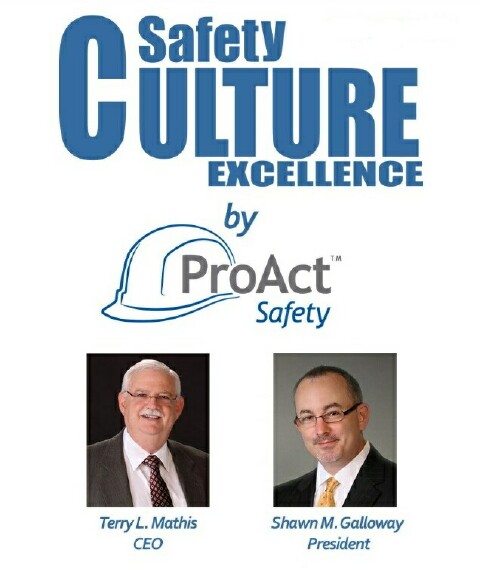
Monday Aug 04, 2014
348 - A Transformational Pareto Analysis Finding Focus
Monday Aug 04, 2014
Monday Aug 04, 2014
Greetings everyone, this podcast recorded while in Orlando, FL. I’d like to share an article I wrote that was published in the July 2014 edition of Professional Safety Magazine. The published article can either be found on the magazine’s website or under Insights at www.ProActSafety.com.
I hope you enjoy the podcast this week. If you would like to download or play on demand our other podcasts, please visit the ProAct Safety’s podcast website at: http://www.safetycultureexcellence.com. If you would like access to archived podcasts (older than 90 days – dating back to January 2008) please visit www.ProActSafety.com/Store. For more detailed strategies to achieve and sustain excellence in performance and culture, pick up a copy of our book, STEPS to Safety Culture Excellence - http://proactsafety.com/insights/steps-to-safety-culture-excellence
Have a great week!
Shawn M. Galloway
ProAct Safety
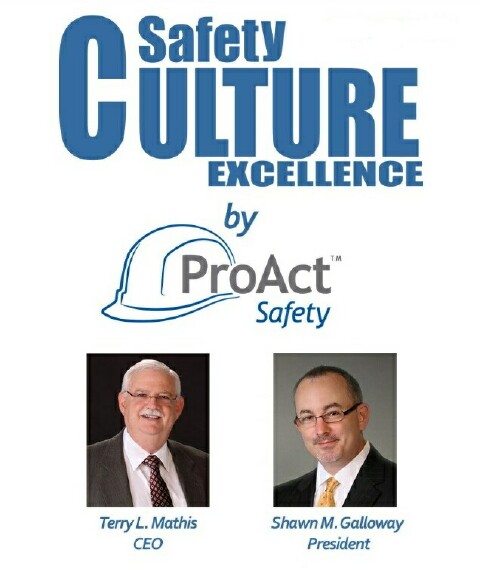
Monday Jul 21, 2014
346 - Measuring Safety Culture Maturity A Better Way
Monday Jul 21, 2014
Monday Jul 21, 2014
This is an audio version of the previously published blog on this topic:
Forget the old ways of measuring safety culture maturity. There
is a new, more effective way to measure cultural maturity and it starts
with looking at the chemistry.

In consulting globally with many of the best in safety performance and culture, nine elements (see the picture with this post) have been identified as most important foci to establish the chemistry which facilitates the necessary climate for a culture of safety excellence to grow. Through consulting engagements and workshops, these nine elements have been successfully leveraged and measured to help organizations identify both their starting point baseline, and also to strategically prioritize which elements to focus on to advance the capabilities of their safety culture.

If you have read my work, participated in any of my workshops or keynote presentations or worked with me directly, you will know I work hard to always provide more take-away tools than motivational fluff. If I was able to provide the framework to facilitate the internal dialogue in article format, I would.
To assist you on your journey to safety excellence, I would like to share this tool with you. To obtain a copy for your internal use, send an email to info@proactsafety.com with the subject of Please Send Chemistry of SCE and our staff will respond at our earliest opportunity.
Cultures will always influence the beliefs and behaviors of employees and contractors as they join the group. You can either manage the chemistry, climate and culture, or the results in any area of operational performance will be managed by them. I invite you to start the conversation to strategically enhance the safety aspect of your company culture and measure your progress by contributed value, not just the lowering of injury rates.
-------------------
Shawn M. Galloway is the President and COO of ProAct Safety. He writes (and tweets:@safetyculture) about his work helping organizations in all industries to achieve and sustain excellence in their culture and performance. He resides near Houston, Texas with his wife and three children.
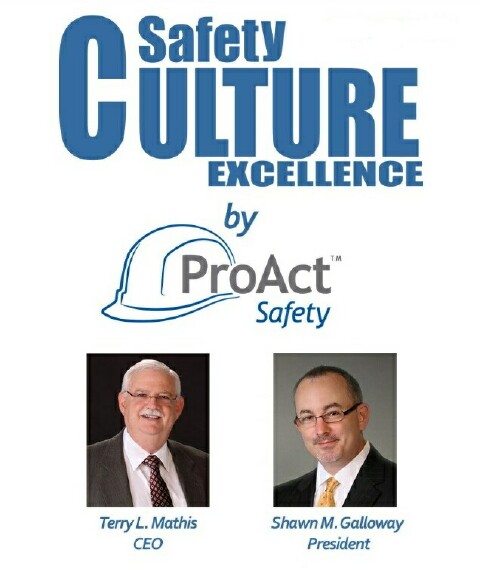
Wednesday Jul 09, 2014
Measuring Safety Culture Maturity: A Better Way
Wednesday Jul 09, 2014
Wednesday Jul 09, 2014
Forget the old ways of measuring safety culture maturity. There is a new, more effective way to measure cultural maturity and it starts with looking at the chemistry.

In consulting globally with many of the best in safety performance and culture, nine elements (see the picture with this post) have been identified as most important foci to establish the chemistry which facilitates the necessary climate for a culture of safety excellence to grow. Through consulting engagements and workshops, these nine elements have been successfully leveraged and measured to help organizations identify both their starting point baseline, and also to strategically prioritize which elements to focus on to advance the capabilities of their safety culture.

If you have read my work, participated in any of my workshops or keynote presentations or worked with me directly, you will know I work hard to always provide more take-away tools than motivational fluff. If I was able to provide the framework to facilitate the internal dialogue in article format, I would.
To assist you on your journey to safety excellence, I would like to share this tool with you. To obtain a copy for your internal use, send an email to info@proactsafety.com with the subject of Please Send Chemistry of SCE and our staff will respond at our earliest opportunity.
Cultures will always influence the beliefs and behaviors of employees and contractors as they join the group. You can either manage the chemistry, climate and culture, or the results in any area of operational performance will be managed by them. I invite you to start the conversation to strategically enhance the safety aspect of your company culture and measure your progress by contributed value, not just the lowering of injury rates.
-------------------
Shawn M. Galloway is the President and COO of ProAct Safety. He writes (and tweets:@safetyculture) about his work helping organizations in all industries to achieve and sustain excellence in their culture and performance. He resides near Houston, Texas with his wife and three children.
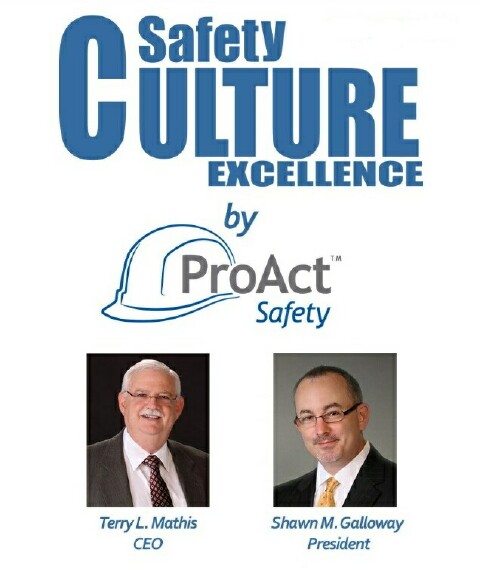
Monday Jun 16, 2014
341 - Who Should Perform Behavior-Based Safety Observations?
Monday Jun 16, 2014
Monday Jun 16, 2014
Greetings everyone, this podcast recorded while in Galveston, TX. I’d like to share an article I wrote that was published May 2014 in BIC Magazine. The published article can either be found on the magazine’s website or under Insights at www.ProActSafety.com.
I hope you enjoy the podcast this week. If you would like to download or play on demand our other podcasts, please visit the ProAct Safety’s podcast website at: http://www.safetycultureexcellence.com. If you would like access to archived podcasts (older than 90 days – dating back to January 2008) please visit www.ProActSafety.com/Store. For more detailed strategies to achieve and sustain excellence in performance and culture, pick up a copy of our book, STEPS to Safety Culture Excellence - http://proactsafety.com/insights/steps-to-safety-culture-excellence
Have a great week!
Shawn M. Galloway
ProAct Safety
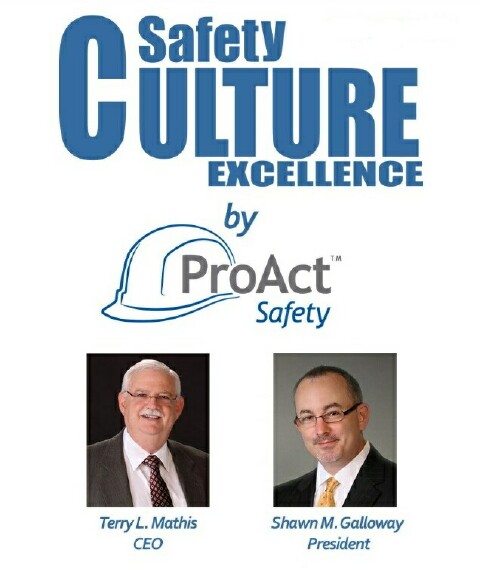
Monday Jun 09, 2014
340 - STEPS to Safety Culture Excellence Workshop
Monday Jun 09, 2014
Monday Jun 09, 2014
A workshop about developing and executing against a comprehensive strategy to significantly enhance injury prevention efforts and measurably evolve the culture, by the thought-leaders at ProAct Safety
Based on the recent book, STEPS to Safety Culture Excellence, the authors will lead this workshop and provide a detailed roadmap on how to develop a three to five year safety excellence business plan. This two-day workshop is limited to ten participants. It would be helpful if each attendee read the book prior to the event to escalate the discovery process.
For more information visit: http://proactsafety.com/events/steps-to-safety-culture-excellence-workshop
Shawn M. Galloway
ProAct Safety
www.ProActSafety.com
www.SafetyCultureExcellence.com
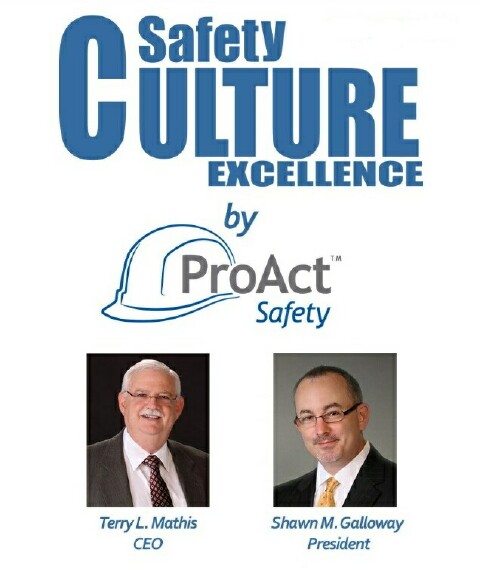
Wednesday Jun 04, 2014
Who is Driving Safety?
Wednesday Jun 04, 2014
Wednesday Jun 04, 2014
The leaders of an organization who were asking for my help to improve their safety efforts told me that they were all pushing safety as hard as they could. I asked them who was driving safety and how long it had been stalled and needing to be pushed. Almost every leadership team is either neglecting, pushing or driving safety. Neglect brings on disaster. The need for pushing often results from previous neglect. Driving safety almost always results in progress and improvement.
Just as the term implies, driving is giving direction, speed and stability to the safety effort. Stalled efforts may require some pushing, but well-running efforts simply need drivers. The most recognized drivers of safety are leadership, supervision, guidelines, and training. Leaders need to give safety strategic direction. Supervisors need to steer and correct the daily efforts. Guidelines, such as rules, procedures, and P.P.E. requirements should provide a road map for the workplace decisions that impact safety. Training should ensure that everyone knows the guidelines and can also recognize and manage the risks in the workplace that may not be fully covered by the guidelines.
Safety efforts that are strategically driven shape the perceptions and culture of the safety efforts. The perceptions and culture combine with the training to shape the daily performance. Supervision keeps the daily performance on track. The daily performance produces the results that are measured by the lagging indicators of safety. If your lagging indicators indicate you are not at your desired destination, ask yourself “who is driving?”
-Terry L. Mathis
For more insights, visit www.ProActSafety.com
Terry L. Mathis is the founder and CEO of ProAct Safety, an international safety and performance excellence firm. He is known for his dynamic presentations in the fields of behavioral and cultural safety, leadership, and operational performance, and is a regular speaker at ASSE, NSC, and numerous company and industry conferences. EHS Today listed Terry as a Safety Guru in ‘The 50 People Who Most Influenced EHS in 2010, 2011 and 2012-2013. He has been a frequent contributor to industry magazines for over 15 years and is the coauthor of STEPS to Safety Culture Excellence, 2013, WILEY.
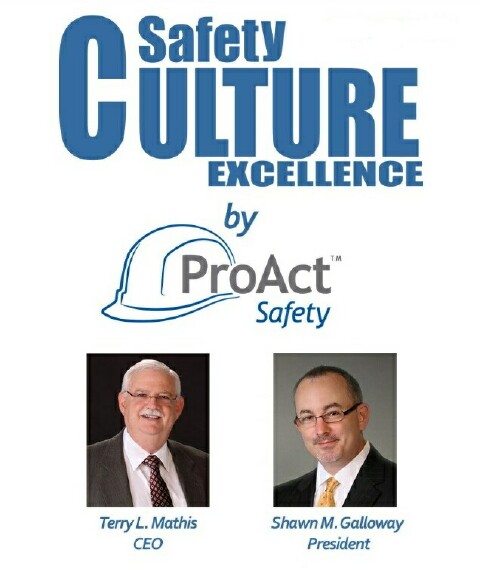
Wednesday May 07, 2014
The Timing and Frequency of Measurement
Wednesday May 07, 2014
Wednesday May 07, 2014
Safety professionals seem to be on a desperate search for “leading indicators.” This is a reaction to a reaction. We have managed safety reactively through injury, incident and near-miss data and are seeking to become more proactive by measuring upstream. This is generally a good trend in thinking that I believe will ultimately look more like a balanced scorecard than simply a dashboard.
However, one topic that is critical but not being discussed is the timing and frequency of measurement. Good metrics help to understand and focus as well as measure performance. If the measurement (or communication of the measurement) is too infrequent or if there is too much time between, the metrics fail to maintain focus. Focus can become habit if reinforced at the right intervals. Some aspects of safety ought to become habitual. The right metrics can aid in the formation of such habits as well as measure the progress toward them.
Certainly there are some aspects of safety that should not become simple habit since they require meticulous planning and execution. But, even these can become common practice with aid of the right metrics and with the right timing and frequency. Metrics that are communicated in a timely and regular basis establish a level of expectation and provide meaningful feedback to maintain and improve performance. Visible progress is also a powerful motivator and can come from well-timed and spaced metrics more naturally, than from artificial incentive and reward systems. When you explore upstream and ask what leading indicators you should measure, also ask how often and regularly you should measure them.
-Terry L. Mathis
Terry L. Mathis is the founder and CEO of ProAct Safety, an international safety and performance excellence firm. He is known for his dynamic presentations in the fields of behavioral and cultural safety, leadership, and operational performance, and is a regular speaker at ASSE, NSC, and numerous company and industry conferences. EHS Today listed Terry as a Safety Guru in ‘The 50 People Who Most Influenced EHS in 2010, 2011 and 2012-2013. He has been a frequent contributor to industry magazines for over 15 years and is the coauthor of STEPS to Safety Culture Excellence, 2013, WILEY.