Episodes
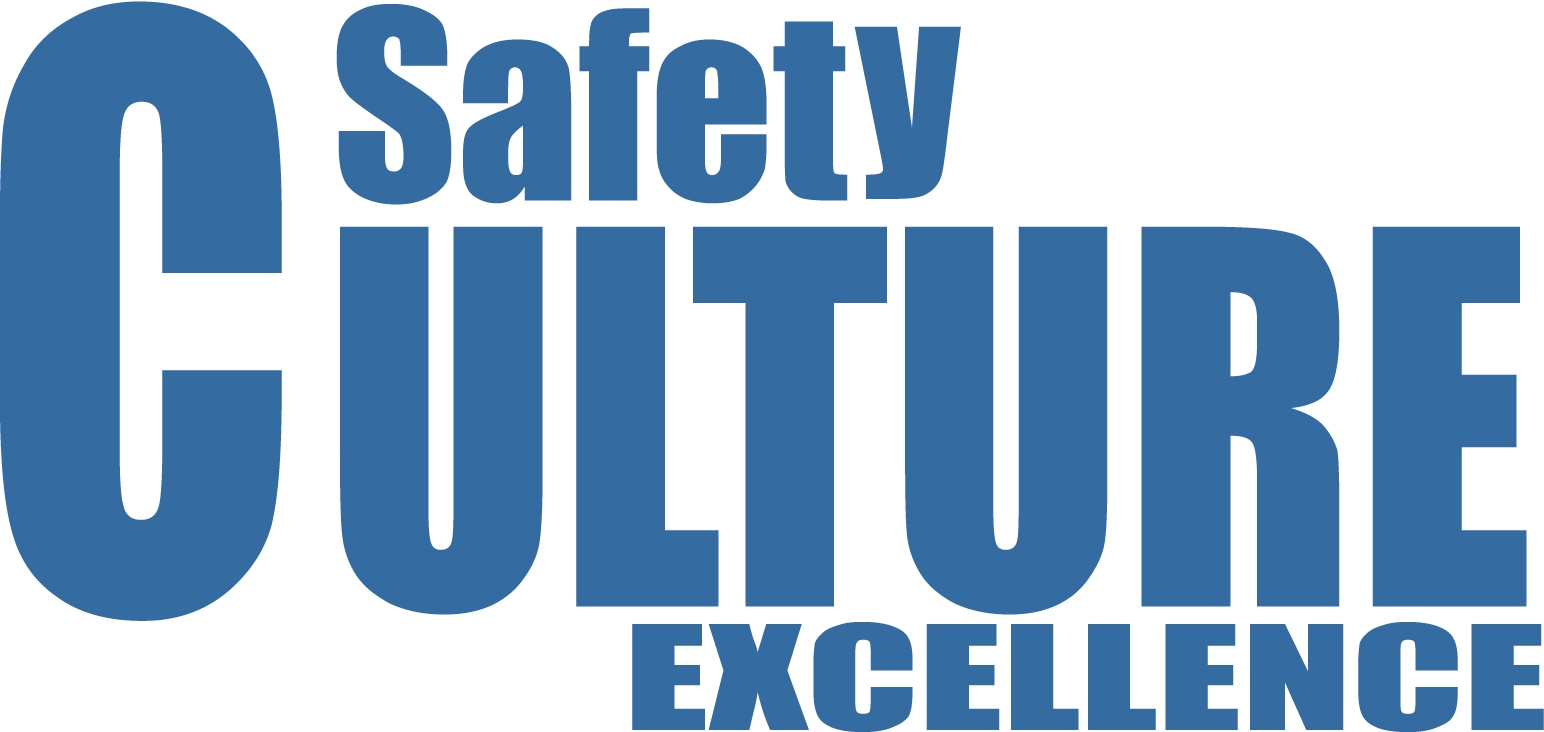
Wednesday Aug 07, 2013
Is Your Organization Oozing Expertise?
Wednesday Aug 07, 2013
Wednesday Aug 07, 2013
The US Census Bureau estimates that 35 million Baby Boomers will be leaving the workplace over the next 10 years or so. If you have these individuals in key positions and lose them all at once, how will that impact your organization? Will they take key safety information with them or will they pass it on before they retire? The answer to that may depend on your planning and the results may be significant.
Many Boomers have been in the same position for years; some for their whole careers. They have knowledge that is not always captured in operating manuals or other documentation. They also have developed judgment about how to handle certain situations based on their years of observation and experience. How can you keep this knowledge and judgment when you lose the people?
One answer is a mentoring program in which experienced workers train new workers. New workers can be asked to capture the tips and procedures they learn and share them with the next generation of workers. Another approach is to have experienced workers hold formal training, develop training materials, or lead JSA or JSOP teams. Still other organizations hire key retirees as part-time consultants or on-call resources for the new employees.
Whatever your plan, your goal should be to spare your organization from oozing out needed expertise as the new generation of workers replace the old.
-Terry L. Mathis
Terry L. Mathis is the founder and CEO of ProAct Safety, an international safety and performance excellence firm. He is known for his dynamic presentations in the fields of behavioral and cultural safety, leadership, and operational performance, and is a regular speaker at ASSE, NSC, and numerous company and industry conferences. EHS Today listed Terry as a Safety Guru in ‘The 50 People Who Most Influenced EHS’ in 2010, 2011 and 2012-2013. He has been a frequent contributor to industry magazines for over 15 years and is the coauthor of STEPS to Safety Culture Excellence, 2013, WILEY.
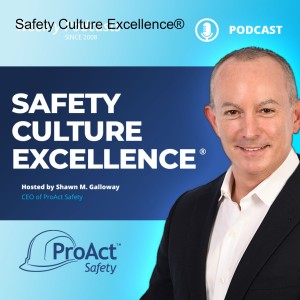
Monday Aug 05, 2013
301 - Accountability: A Dirty Word in Safety
Monday Aug 05, 2013
Monday Aug 05, 2013
Greetings everyone, this podcast recorded while in Prattville, Alabama. I’d like to share an article I wrote, published April 2013 in Occupational Health & Safety Magazine. It was titled, Accountability: A Dirty Word in Safety. The published article can either be found on the magazine’s website or under Insights at www.ProActSafety.com. I hope you enjoy the podcast this week. If you would like to download or play on demand our other podcasts, please visit the ProAct Safety’s podcast website at: http://www.safetycultureexcellence.com. If you would like access to archived podcasts (older than 90 days – dating back to January 2008) please visit www.ProActSafety.com/Store. For more detailed strategies to achieve and sustain excellence in performance and culture, pick up a copy of our book, STEPS to Safety Culture Excellence - http://proactsafety.com/insights/steps-to-safety-culture-excellence Have a great week! Shawn M. Galloway ProAct Safety, Inc
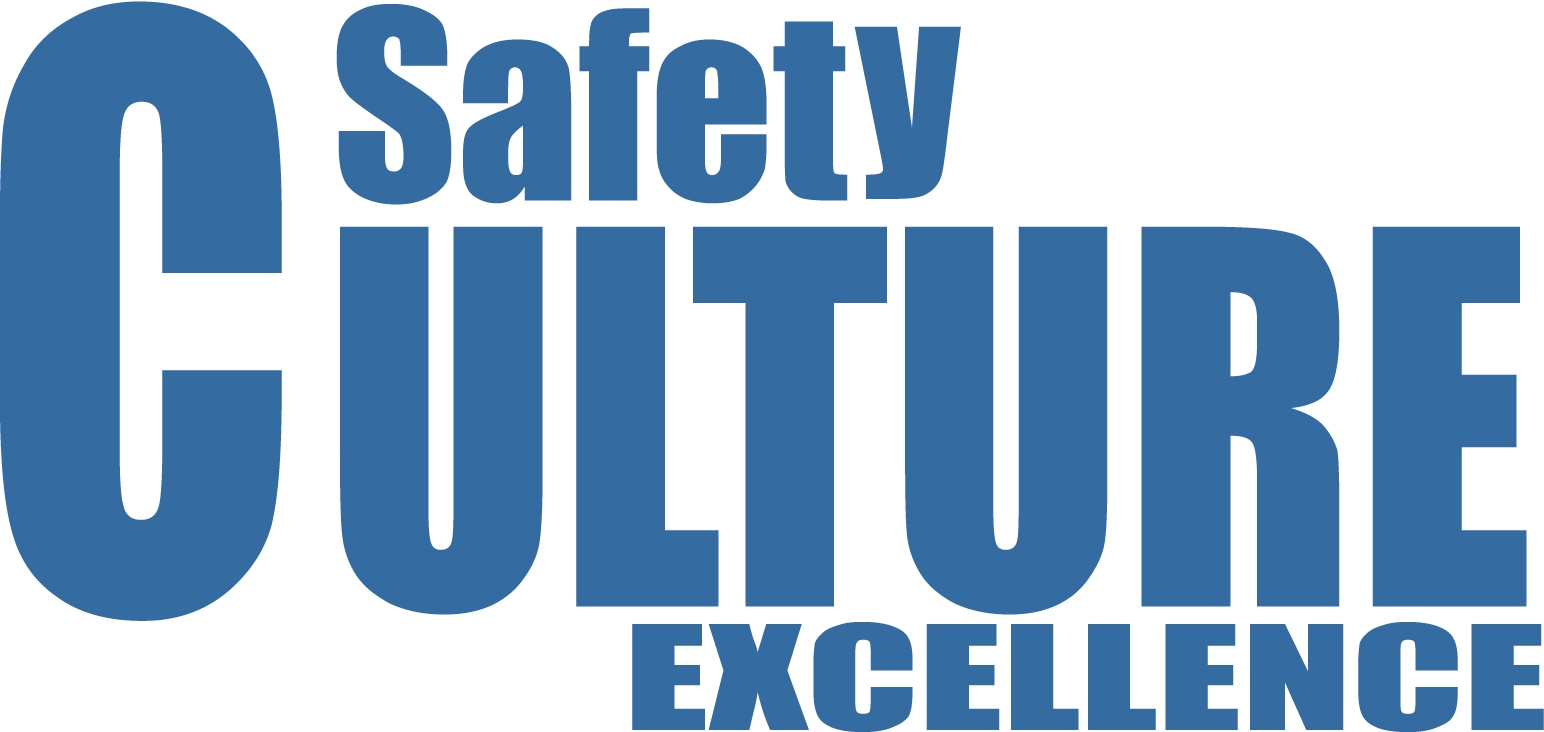
Wednesday Jul 31, 2013
Divided Management Creates Conflicting Priorities
Wednesday Jul 31, 2013
Wednesday Jul 31, 2013
Almost all jobs involve multiple priorities. If you have one boss who helps you balance these priorities, it becomes more and more clear how to do so. When workers see how their boss handles multiple priorities and get feedback on their own handling of them, they get a feel for the relative importance of each.
However, when different aspects of business are managed or supervised by different people, there will inevitably be a conflict of priorities. If one person supervises production, another supervises quality, and another supervises safety, there is not only a conflict of three priorities, but of three people. Workers now must juggle multiple priorities as well as multiple personalities and relationships. It is difficult to see the unity of priorities when the organization divides them into different departments and personnel. The big picture tends to be a divided screen with three pictures. The worker can only watch one at a time.
It is critically important for organizations to balance and unify, not divide priorities. Most organizations want safe, quality production, not three conflicting aspects of work. It is fine to have experts in each field who advise and serve as resources. It is not good to try to make such experts partial supervisors on the shop floor. One supervisor can better manage the whole process and unify the aspects of the process where workers view their role as doing the work, rather than refereeing their multiple bosses.
-Terry L. Mathis
Terry L. Mathis is the founder and CEO of ProAct Safety, an international safety and performance excellence firm. He is known for his dynamic presentations in the fields of behavioral and cultural safety, leadership, and operational performance, and is a regular speaker at ASSE, NSC, and numerous company and industry conferences. EHS Today listed Terry as a Safety Guru in ‘The 50 People Who Most Influenced EHS’ in 2010, 2011 and 2012-2013. He has been a frequent contributor to industry magazines for over 15 years and is the coauthor of STEPS to Safety Culture Excellence, 2013, WILEY.
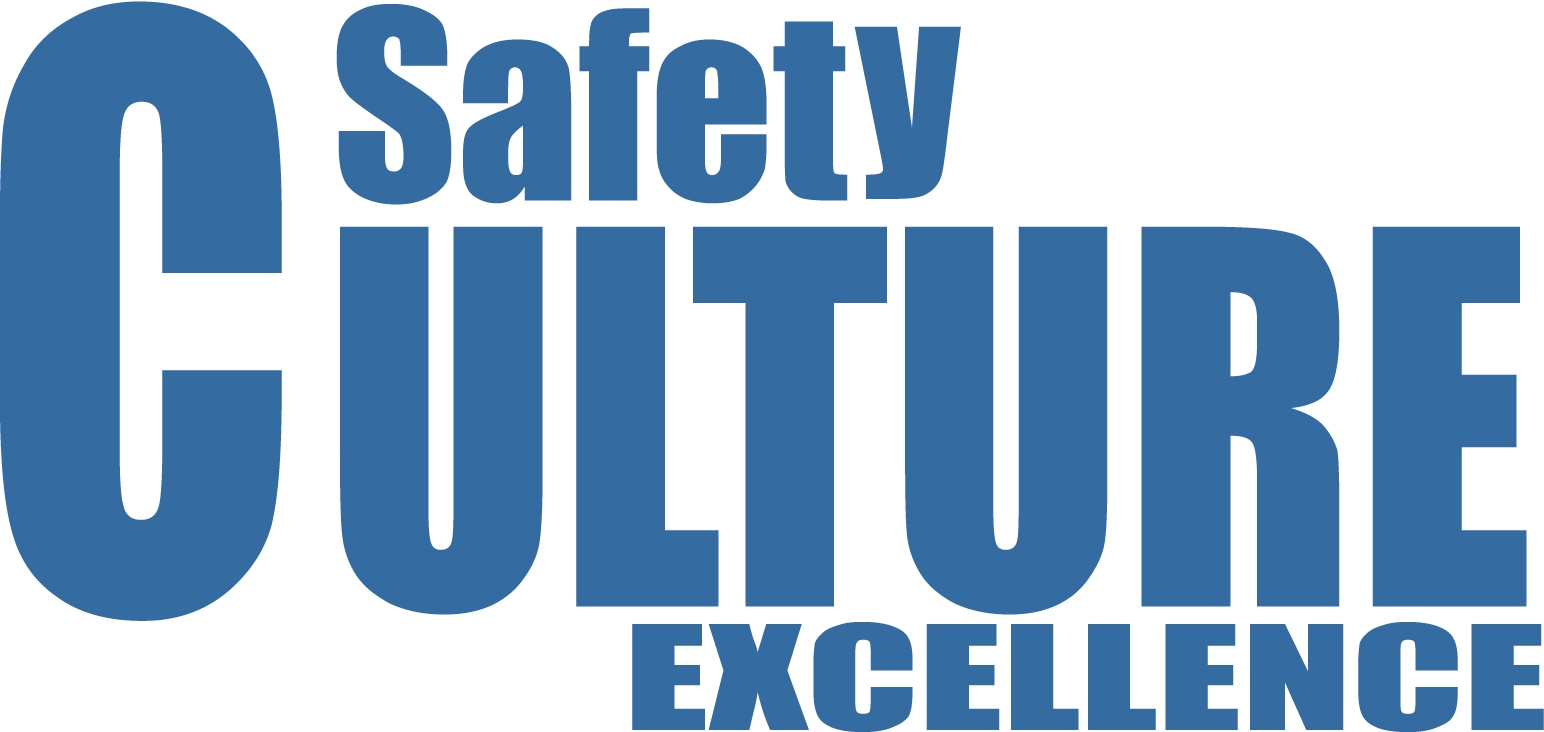
Wednesday Jul 17, 2013
The Bandwidth of Safety Management: How much can you do at once?
Wednesday Jul 17, 2013
Wednesday Jul 17, 2013
One of the most common mistakes organizations and safety professionals make is to try to do too much at once. It seems logical that more safety-related activities should create better safety awareness and thus result in improved safety performance. This is seldom what happens. Too much at once results in overload and also blocks internalization of important safety principles and practices. Trying to eat the elephant in one bite chokes the eater and aggravates the elephant.
Human attention, like the internet has limited bandwidth. It can only handle a certain amount of information at once. More is not better, it is lost. When organizations and safety professionals focus on specific and well prioritized improvement targets, the human attention machine works well. New precautions are understood and internalized. As the new safety habits and thinking progress, new targets can be added. The organization sees the elephant disappearing a bite at a time and that further motivates progress.
It requires discipline and clear thinking to realize that more is not better and that slower can actually be faster. But keeping safety efforts within the proper bandwidth of the human brain is the best and ultimately fastest path to safety excellence.
-Terry L. Mathis
Terry L. Mathis is the founder and CEO of ProAct Safety, an international safety and performance excellence firm. He is known for his dynamic presentations in the fields of behavioral and cultural safety, leadership, and operational performance, and is a regular speaker at ASSE, NSC, and numerous company and industry conferences. EHS Today listed Terry as a Safety Guru in ‘The 50 People Who Most Influenced EHS’ in 2010, 2011 and 2012-2013. He has been a frequent contributor to industry magazines for over 15 years and is the coauthor of STEPS to Safety Culture Excellence, 2013, WILEY.
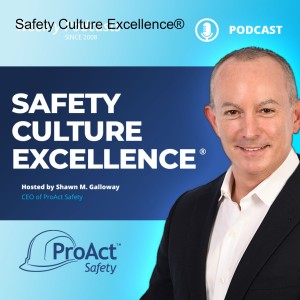
Monday Jul 15, 2013
298 - Who Says "Go"? Is Safety Led or Abdicated?
Monday Jul 15, 2013
Monday Jul 15, 2013
Greetings everyone, this podcast recorded while in Shreveport, LA. I’d like to share an article Terry Mathis wrote, published March 2013 in EHS Today Magazine. It was titled, Who Says "Go"? Is Safety Led or Abdicated? The published article can either be found on the magazine’s website or under Insights at www.ProActSafety.com. I hope you enjoy the podcast this week. If you would like to download or play on demand our other podcasts, please visit the ProAct Safety’s podcast website at: http://www.safetycultureexcellence.com. If you would like access to archived podcasts (older than 90 days – dating back to January 2008) please visit www.ProActSafety.com/Store. For more detailed strategies to achieve and sustain excellence in performance and culture, pick up a copy of our book, STEPS to Safety Culture Excellence - http://proactsafety.com/insights/steps-to-safety-culture-excellence Have a great week! Shawn M. Galloway ProAct Safety, Inc
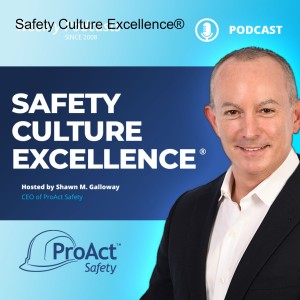
Monday Jul 08, 2013
297 - Challenging the Goal of Safety
Monday Jul 08, 2013
Monday Jul 08, 2013
Greetings everyone, this podcast recorded while in Bastrop, Texas. I’d like to share an article I wrote that was published March 2013 in QHSE Focus Magazine. It was titled, Challenging the Goal of Safety. The published article can either be found on the magazine’s website or under Insights at www.ProActSafety.com. I hope you enjoy the podcast this week. If you would like to download or play on demand our other podcasts, please visit the ProAct Safety’s podcast website at: http://www.safetycultureexcellence.com. If you would like access to archived podcasts (older than 90 days – dating back to January 2008) please visit www.ProActSafety.com/Store. For more detailed strategies to achieve and sustain excellence in performance and culture, pick up a copy of our book, STEPS to Safety Culture Excellence - http://proactsafety.com/insights/steps-to-safety-culture-excellence Have a great week! Shawn M. Galloway ProAct Safety, Inc
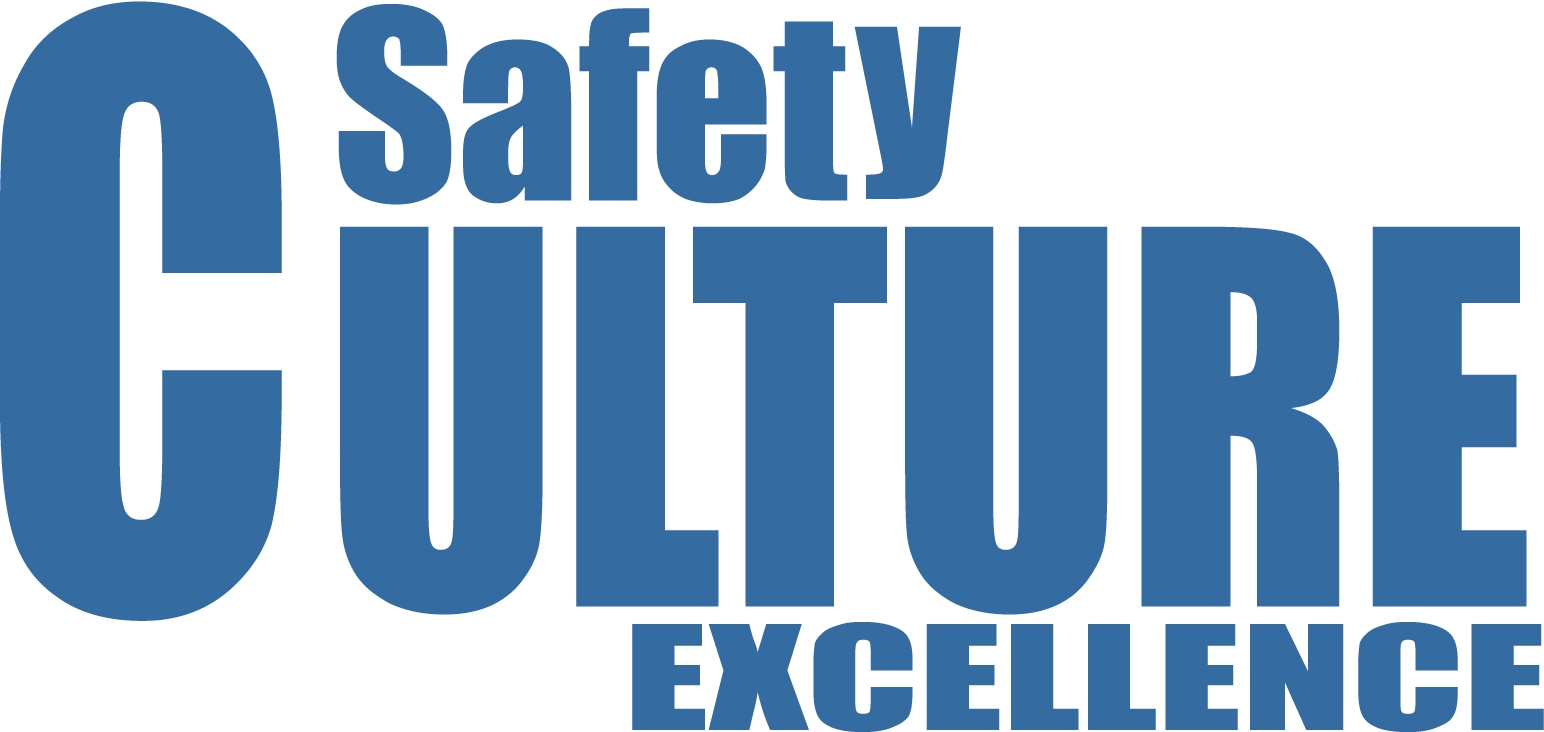
Wednesday Jun 26, 2013
Do Your Accidents Have Special or Common Cause?
Wednesday Jun 26, 2013
Wednesday Jun 26, 2013
W. Edwards Deming explained a basic concept of manufacturing quality by elaborating on the cause of defects. He explained that some defects had special cause (i.e., some unusual event caused the defect to happen). Other defects happened due to causes that are built into the manufacturing processes itself. He called these common causes.
There is a debate among safety professionals these days about whether accidents are caused more by system issues or simply by human error. The simple fact is that it could be either and that neither is mutually exclusive. Your organization could be having accidents caused by either or both. Finding out the cause is critical during accident investigations and making the distinction between common and special causes can be very useful.
This dichotomy is less useful for fixing blame than it is for fixing problems. Special causes alert us to outside forces to guard against in the future. We can often extend our caution beyond the specific issue to other similar risks or situations. When a foreign object gets into a product, we can protect against that object but also explore what other objects could find their way into our processes and how they could do so. When a special outside issue impacts safety, we can use similar reasoning to increase our awareness and precautions against such risks.
Common causes can be more difficult to recognize because they hide within our systems and influence other actions and decisions that can directly lead to defects and/or accidents. However, it is critical to identify them because they will continue to influence risks until we see and address them. Even what looks like simple human error can be influenced by systems issues. This is one reason for always asking “why?” to find what may lie beyond worker decisions and actions.
Deming left us with a warning about finding out and classifying causes. He said that blame causes fear and that fear causes the hiding and skewing of information critical to understanding causation. We should seek first to understand and then take intelligent action based on that understanding.
-Terry L. Mathis
Terry L. Mathis is the founder and CEO of ProAct Safety, an international safety and performance excellence firm. He is known for his dynamic presentations in the fields of behavioral and cultural safety, leadership, and operational performance, and is a regular speaker at ASSE, NSC, and numerous company and industry conferences. EHS Today listed Terry as a Safety Guru in ‘The 50 People Who Most Influenced EHS’ in 2010, 2011 and 2012-2013. He has been a frequent contributor to industry magazines for over 15 years and is the coauthor of STEPS to Safety Culture Excellence, 2013, WILEY.
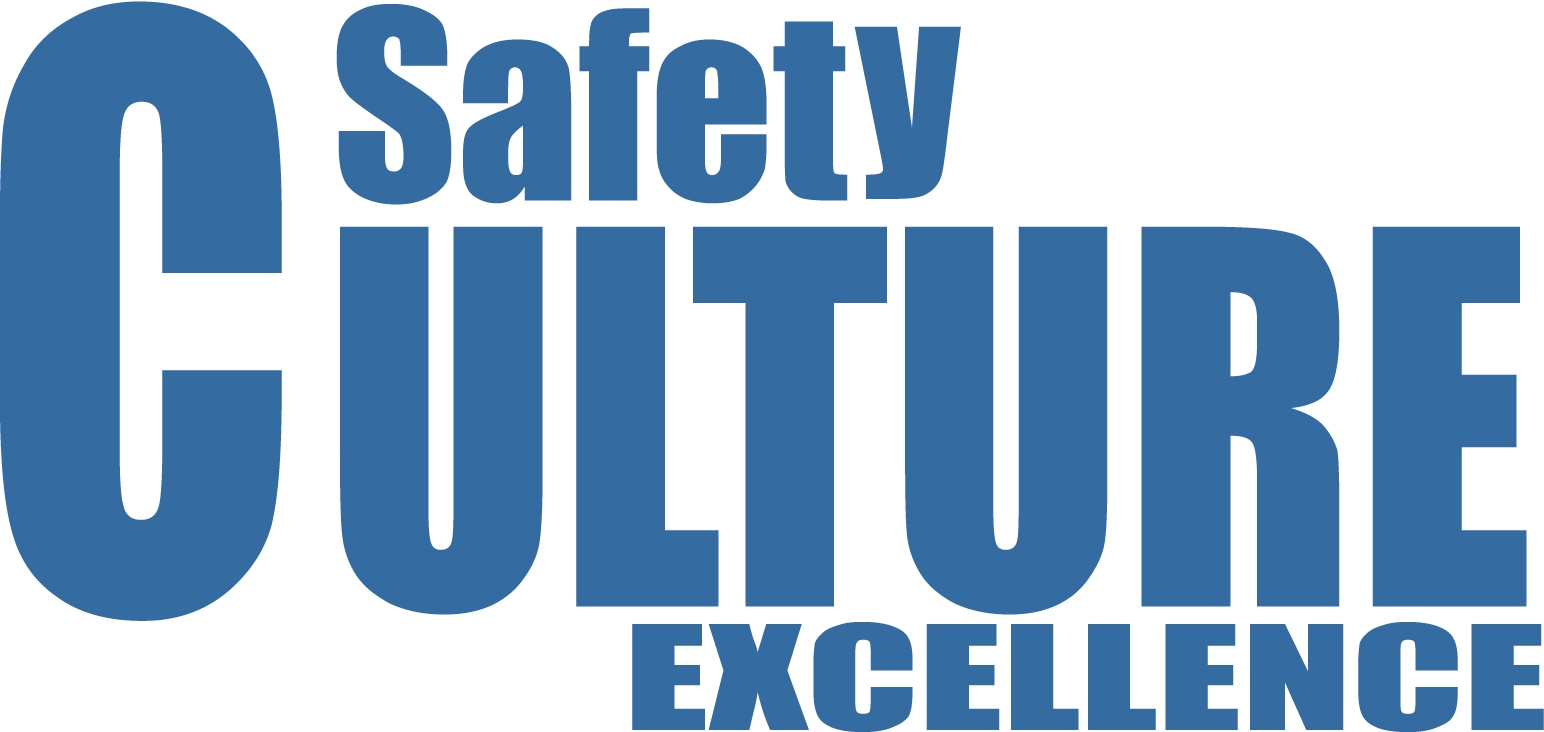
Wednesday Jun 19, 2013
Safety Thinking vs. Safety Habits
Wednesday Jun 19, 2013
Wednesday Jun 19, 2013
In safety there are issues that require a lot of thought and decision making. There are others that only require simple action. These simple actions should be trained as habits and programmed into the auto pilot of workers. It is a total waste of time to muse over whether or not to buckle a seatbelt. Just make buckling an automatic response that is done every time without though or debate. However, don’t allow the engineering crew to refuel the nuclear reactor by habit. Even if the process has steps that are repeated regularly, plan and carry them out very consciously. Analyze the issues and keep everyone on their guard mentally as the process is completed. Check and recheck each step and make sure everyone involved feels free to offer suggestions and voice concerns. Hold a wrap-up meeting to review and ensure that everything is complete and secure before ending the project. Organizations with excellent safety performance recognize this dichotomy. It is critical to differentiate the precautions that require mindless action and those that require careful planning and execution. Confusing one for the other can spell disaster. -Terry L. Mathis Terry L. Mathis is the founder and CEO of ProAct Safety, an international safety and performance excellence firm. He is known for his dynamic presentations in the fields of behavioral and cultural safety, leadership, and operational performance, and is a regular speaker at ASSE, NSC, and numerous company and industry conferences. EHS Today listed Terry as a Safety Guru in ‘The 50 People Who Most Influenced EHS’ in 2010, 2011 and 2012-2013. He has been a frequent contributor to industry magazines for over 15 years and is the coauthor of STEPS to Safety Culture Excellence, 2013, WILEY.
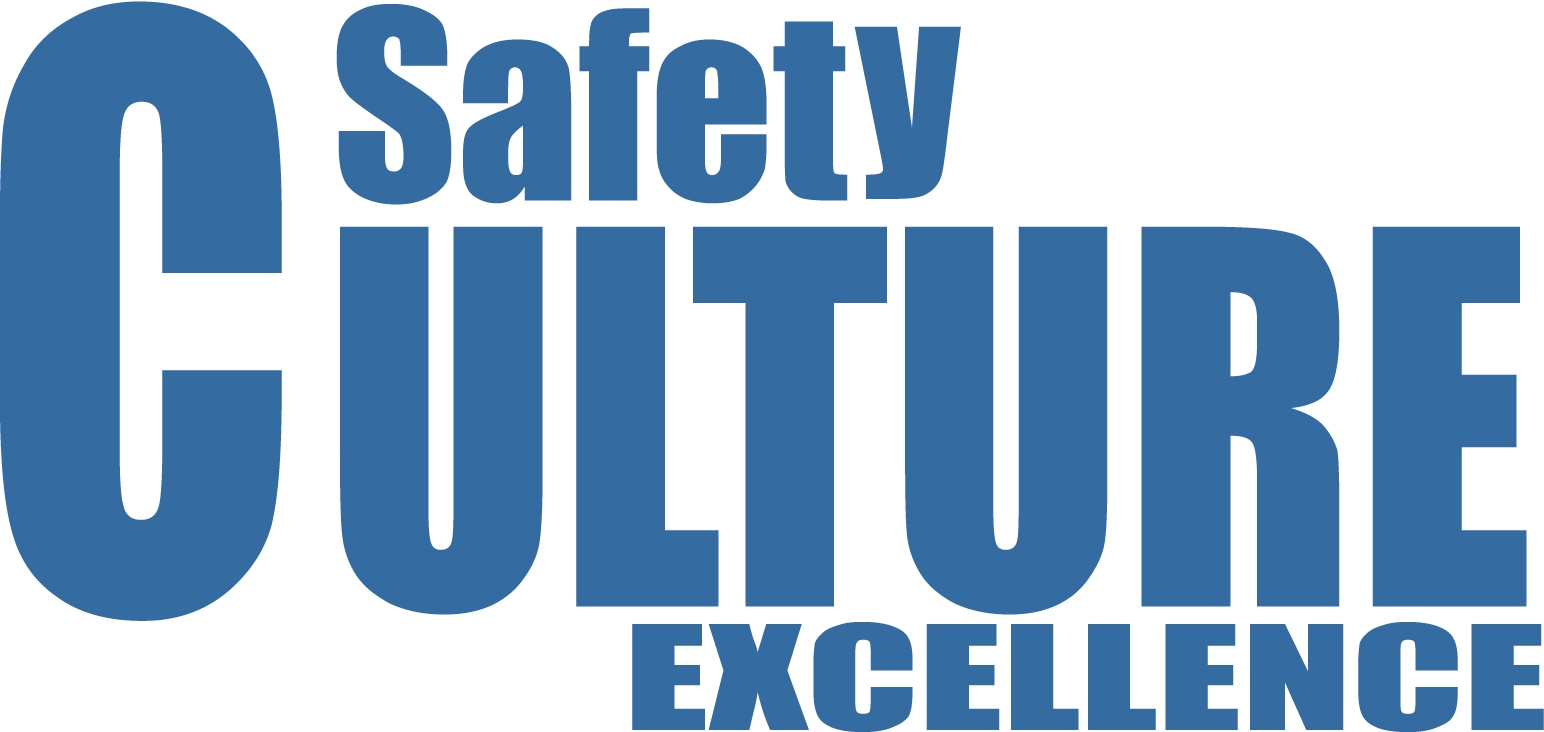
Wednesday Jun 12, 2013
Is Your Safety Effort Surviving or Thriving
Wednesday Jun 12, 2013
Wednesday Jun 12, 2013
Maslow pointed out that we focus on immediate needs until they are met and then move on to higher goals. Is your safety program still focused on where the next meal is coming from or looking for enlightenment? There is no ideal answer to this question; only an honest one. If you are still struggling to get your workers into basic compliance (i.e. Knowing and following the rules and procedures), you are trying to survive. If you are well past that stage and looking for the next step change beyond your already good results, you are trying to thrive. There is no fault in either case. You probably inherited the current state and are challenged to take it to the next level. What is important is that you recognize your current state and respond accordingly. If you are in survival mode, it is imperative that your supervisors are respected and viewed by workers as friends and not foes. Position and authority don’t matter as much to workers trying to survive as the distinction between friend and foe. Friends are trying to help you survive; foes are trying to make you fail. Workers will follow their friends and not their foes. It is also critically important that you communicate accident data as stories from which you can learn lessons. Survivalists view risk taking as necessary to survival and don’t generalize well. Tell them the story of the accident and let them determine lessons learned from the story. In thrive mode, you need to focus on the passion and purpose of safety excellence. To be excellent, it is not enough to convince workers; you must convert them. Directives will get hands and feet moving. It takes passion to move hearts and minds. It is critically important to recognize the difference and to address it intelligently. Many safety professionals think that more of the same will get them to the next level. Unfortunately, that is seldom the case. The tools of excellence are different from the tools of pretty good. You can be the voice of reason and get the organization from bad to good. You have to be an inspirational leader to get from good to great. -Terry L. Mathis Terry L. Mathis is the founder and CEO of ProAct Safety, an international safety and performance excellence firm. He is known for his dynamic presentations in the fields of behavioral and cultural safety, leadership, and operational performance, and is a regular speaker at ASSE, NSC, and numerous company and industry conferences. EHS Today listed Terry as a Safety Guru in ‘The 50 People Who Most Influenced EHS’ in 2010, 2011 and 2012-2013. He has been a frequent contributor to industry magazines for over 15 years and is the coauthor of STEPS to Safety Culture Excellence, 2013, WILEY.
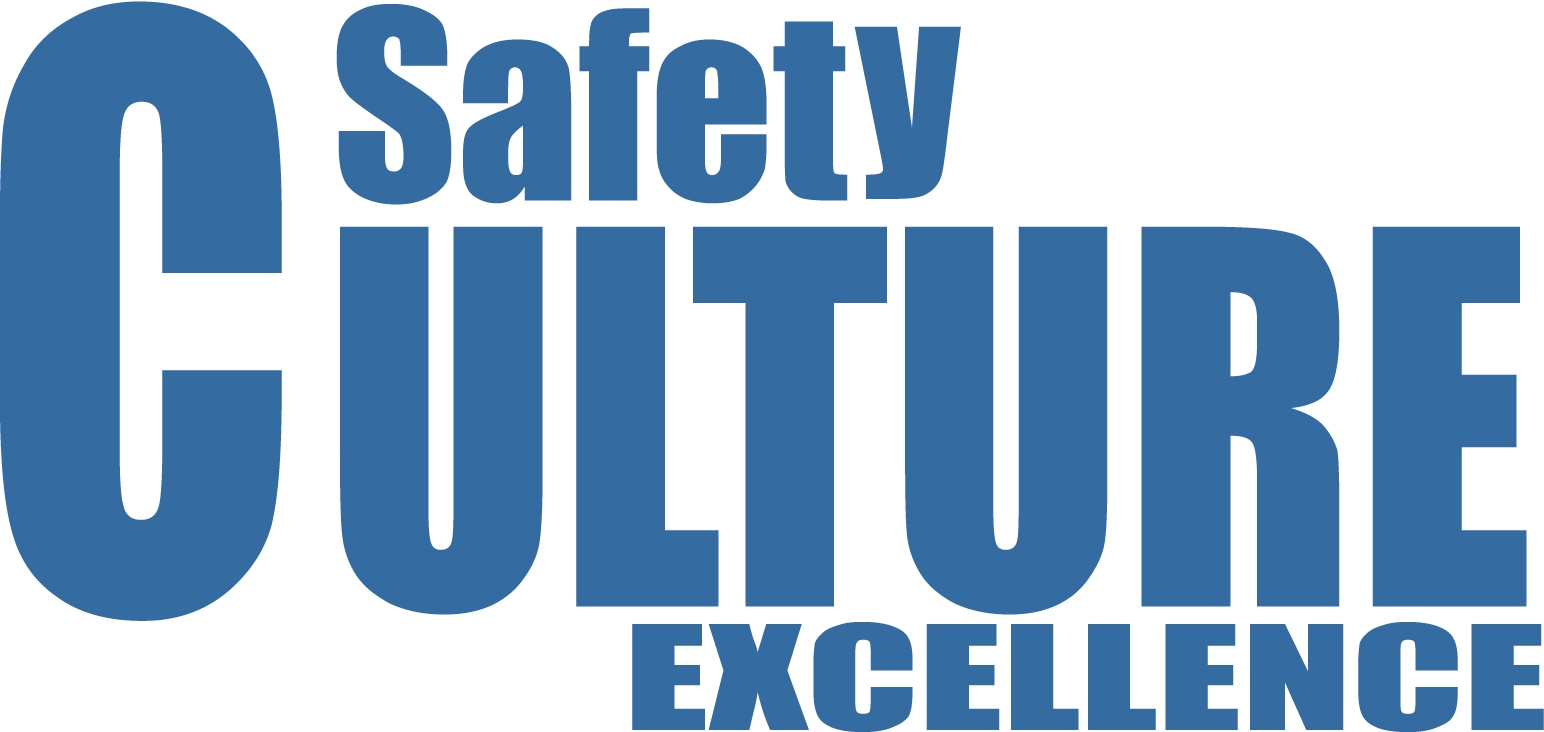
Wednesday May 22, 2013
Going Out on a Limb for Safety
Wednesday May 22, 2013
Wednesday May 22, 2013
I thinned some trees in a thick, forested area on my lot hoping the remaining trees would grow more wide limbs and spread their canopies. It didn’t happen. I asked my tree expert why not and he explained that new limbs on a mature tree were only growing out of the bark and not the core of the tree trunk. They were weak and seldom reached large size without breaking off in the first strong wind. Many safety programs likewise are add-ons and have no real connection to the core values and strategies of the organization. We hope they will provide extra coverage and fill the gaps, but they seldom survive for very long. The strong limbs of our safety programs are connected to a solid strategy and designed to provide specific coverage. They are not afterthoughts, but the result of solid planning. It is crucial for organizational leaders to think of the tree and the limbs as one unit. If safety is a core value of the organization, there are no safety goals; only business goals related to safety. The strategy of the organization includes safety-related strategies that connect to the core. Leaders might fertilize the soil and stimulate the roots, but they don’t try to artificially graft on limbs that aren’t firmly connected. Many safety programs and processes are attempts to compensate for a lack of core strategy and seldom survive the winds of change. -Terry L. Mathis Terry L. Mathis is the founder and CEO of ProAct Safety, an international safety and performance excellence firm. He is known for his dynamic presentations in the fields of behavioral and cultural safety, leadership, and operational performance, and is a regular speaker at ASSE, NSC, and numerous company and industry conferences. EHS Today listed Terry as a Safety Guru in ‘The 50 People Who Most Influenced EHS’ in both 2010 and 2011. He has been a frequent contributor to industry magazines for over 15 years and is the coauthor of STEPS to Safety Culture Excellence, 2013, WILEY.