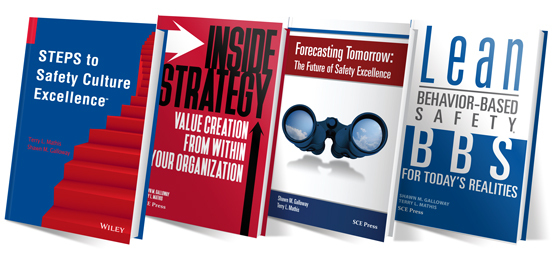
STEPS to Safety Culture Excellence
STEPS to Safety Culture Excellence is based on the authors' firsthand experience working with international organizations in every major industry that have successfully developed and implemented ongoing cultures of safety excellence. Whether your organization is a small regional firm or a large multinational corporation, you'll find that the STEPS process enables you to instill Safety Culture Excellence within your organization. STEPS (Strategic Targets for Excellent Performance in SafetySM) demystifies the process of developing Safety Culture Excellence by breaking it down into small logical, internally led tasks.
To download the introduction, view the webinar or for purchase options, please visit: https://proactsafety.com/insights/book-steps-to-safety-culture-excellence.
Is Your Safety Strategy Ready for What's Coming? The marketplace and allocation of internal resources are both increasingly competitive. Safety strategies of the future must align with evolving business goals. Will your company's safety efforts keep up with the demands of the future? Emerging trends are becoming increasingly visible regarding how safety is viewed, thought of, strategically managed, and how progress is measured. Moreover, the cast of characters, the roles they play, and accountability for responsibilities are evolving, all for the better.
Ask any two people what strategy is and you're likely to get two different answers. Ask those same two people how strategic thinking generates value at all levels from within an organization and you'll probably be met with blank stares. Ever since strategy gained currency as an organizational concept in the 1960s, there's been confusion about how to define it. Strategy isn't a detailed plan of action. nor is it a corporate vision, or an objective, or a mission statement. Strategy is not what to think. It's how to think.
In 2001, ProAct Safety introduced Lean BBS® as a major update to traditional behavior-based safety (BBS) models with a focus on providing new value with more efficient, safer work. Simply put, Lean BBS focuses on adding value to employees rather than trying to control them.
Lean BBS addresses the four major issues found within the average behavior-based safety process:
- BBS provides successful results for many organizations, but they are looking for a way to take the process to the next level. The Lean BBS methodology takes them there.
- Some are adamantly against BBS for a number of reasons (union resistance, questionable implementations, cookie-cutter and inflexible approaches, etc.). Lean BBS gains bargaining unit support, is fit-for-purpose and customized to the realities of each organization.
- Organizations with vastly different processes from site to site want to bring uniformity across the company. Simply changing from one methodology to another is not appealing nor rational. Implementing a more efficient Lean BBS model was both appealing and a rational solution to encourage the processes to evolve towards value-add.
- Some hesitate to pursue BBS due to high costs and demand on internal resources to operate the process. Lean BBS provides an alternative that addresses these concerns due to the hyper focus on efficiency and ensuring value-add.