Episodes
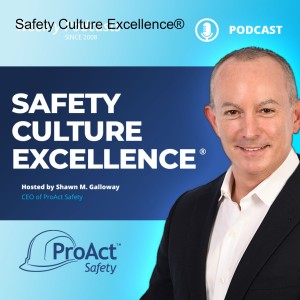
Monday May 20, 2024
809: Software for Behavior-Based Safety
Monday May 20, 2024
Monday May 20, 2024
See all our books available in all formats on Amazon.
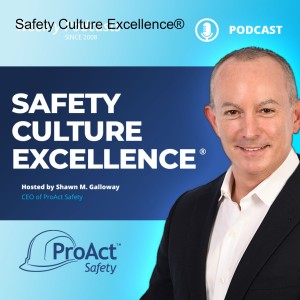
Monday Sep 18, 2023
776: Observing Conditions and Behaviors
Monday Sep 18, 2023
Monday Sep 18, 2023

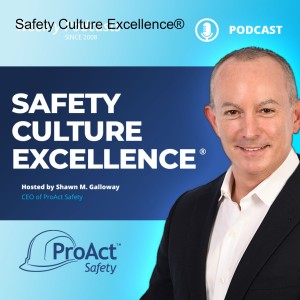
Monday Sep 04, 2023
774: Not Paying Attention
Monday Sep 04, 2023
Monday Sep 04, 2023

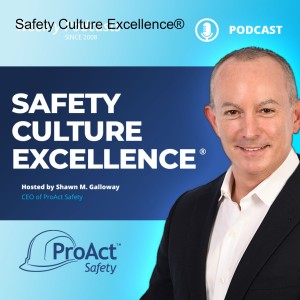
Monday Sep 20, 2021
708: Black Holes
Monday Sep 20, 2021
Monday Sep 20, 2021
Hello, welcome to the Safety Culture Excellence podcast, brought to you by ProAct Safety, the world leader of safety excellence.

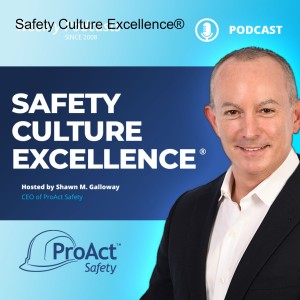
Monday Jan 11, 2021
673: Actionable Data
Monday Jan 11, 2021
Monday Jan 11, 2021
Hello, welcome to the Safety Culture Excellence podcast, brought to you by ProAct Safety, the world leader of safety excellence.

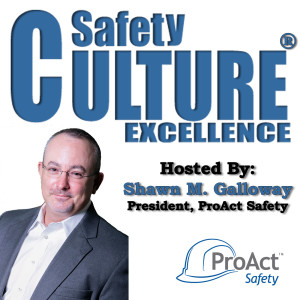
Monday Oct 15, 2018
565: Safety - Seeing or Thinking
Monday Oct 15, 2018
Monday Oct 15, 2018

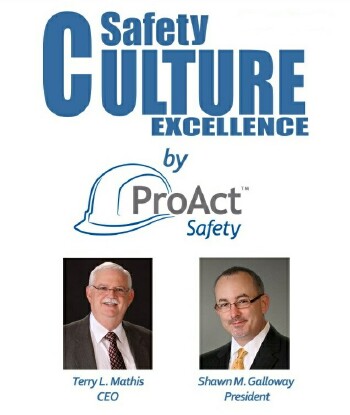
Wednesday Apr 29, 2015
Peeling the Onion: Solving Safety Problems One Layer at a Time
Wednesday Apr 29, 2015
Wednesday Apr 29, 2015
During a safety observation, workers were observed using the wrong tool for a job, which created a risk. When a safety committee saw the report, they petitioned management to buy the proper tool for the work station. The committee member who received the tool took it to the work station and presented it to the worker on shift with an explanation of what had happened and the action taken. The worker admitted that he really had not been taught what the proper tool was for the job and had used the home-made tool since he began his job.
The next month’s observations reported that workers were still using the wrong tool for the job. Follow-up revealed that workers on the other shifts had not received the communication and were not aware of the new tool. The safety committee made sure that every worker was made aware of the proper tool in safety and tool box meetings and felt sure the next month’s data would show the problem solved.
The next month, the observations showed the workers were STILL not using the right tool. Follow-up revealed that workers had formed the habit of using the wrong tool and that the habit was not changed. The safety committee developed a plan to remind workers and, within the next few months, the problem was truly solved.
Lessons learned:
• Safety problems can be multi-layered and require multiple fixes.
• Solving problems requires follow-up.
• Influences need to be addressed in order to change the behavior.
-Terry L. Mathis
For more insights, visit
www.ProActSafety.com
Terry L. Mathis is the founder and CEO of ProAct Safety, an international safety and performance excellence firm. He is known for his dynamic presentations in the fields of behavioral and cultural safety, leadership, and operational performance, and is a regular speaker at ASSE, NSC, and numerous company and industry conferences. EHS Today listed Terry as a Safety Guru in ‘The 50 People Who Most Influenced EHS three consecutive times. He has been a frequent contributor to industry magazines for over 15 years and is the coauthor of STEPS to Safety Culture Excellence (2013, WILEY).
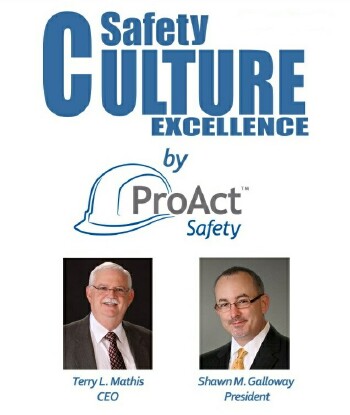
Monday Apr 20, 2015
384 - Seeing the Right Moves: The Key to Reducing Risks
Monday Apr 20, 2015
Monday Apr 20, 2015

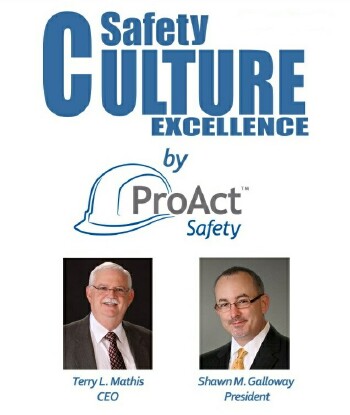
Wednesday Jan 21, 2015
Quantity and Quality
Wednesday Jan 21, 2015
Wednesday Jan 21, 2015
Rule of thumb: Any quantity goal without a quality requirement will encourage “pencil whipping”. This is especially true of safety audits and observations. Organizations that require everyone to do two observations per month or two audits per week are misstating what they truly want. Quantity is ineffective without quality. There are thousands of studies that support the idea that a certain quantity of contact or assessment is necessary for improvements. But they all go out the window if the numbers are filled with fake, or otherwise poor-quality, components.
What drives change is the right number of quality contacts. Going through the motions and getting the numbers just to check off a box is not what organizations really want. So why do they set these goals, omitting the quality requirements? Largely because the quantity is easily and discretely measured while the quality is more complicated and subjective. It is easier to create accountability around numbers than quality, but doing so can completely compromise the effort. State both quantity and quality requirements in all goals and do your best to hold workers accountable for both.
-Terry L. Mathis
For more insights, visit
Terry L. Mathis is the founder and CEO of ProAct Safety, an international safety and performance excellence firm. He is known for his dynamic presentations in the fields of behavioral and cultural safety, leadership, and operational performance, and is a regular speaker at ASSE, NSC, and numerous company and industry conferences. EHS Today listed Terry as a Safety Guru in ‘The 50 People Who Most Influenced EHS three consecutive times. He has been a frequent contributor to industry magazines for over 15 years and is the coauthor of STEPS to Safety Culture Excellence (2013, WILEY).
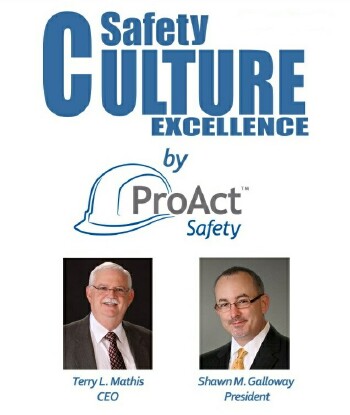
Monday Jan 19, 2015
371 - Misunderstanding Hazards and Risks
Monday Jan 19, 2015
Monday Jan 19, 2015
